
WHAT MAKES AN ISLAND?
WOOD
It’s the bones of the instrument.
Every single piece of wood that makes it onto one of my instruments is hand selected. From rummaging through boards at the lumber yard to find the perfect piece, to working closely with suppliers across the country with whom I’ve built decade-plus-long relationships, I make sure that each piece of wood is perfect for a given instrument.
It may be almost negligible for the individual builder in the face of giant corporations and factories, but I still believe it is our responsibility to take care of our planet and its resources. For that reason, I prefer to build with domestic, salvaged and reclaimed timber whenever possible.
I also think there’s something very special about being able to take a piece of wood with 100+ years of history and giving it a second life and a chance to tell a whole new story. I use exotics sparingly, though they do have their place.
I’m also constantly looking towards new engineered alternative materials and excited about their developments.
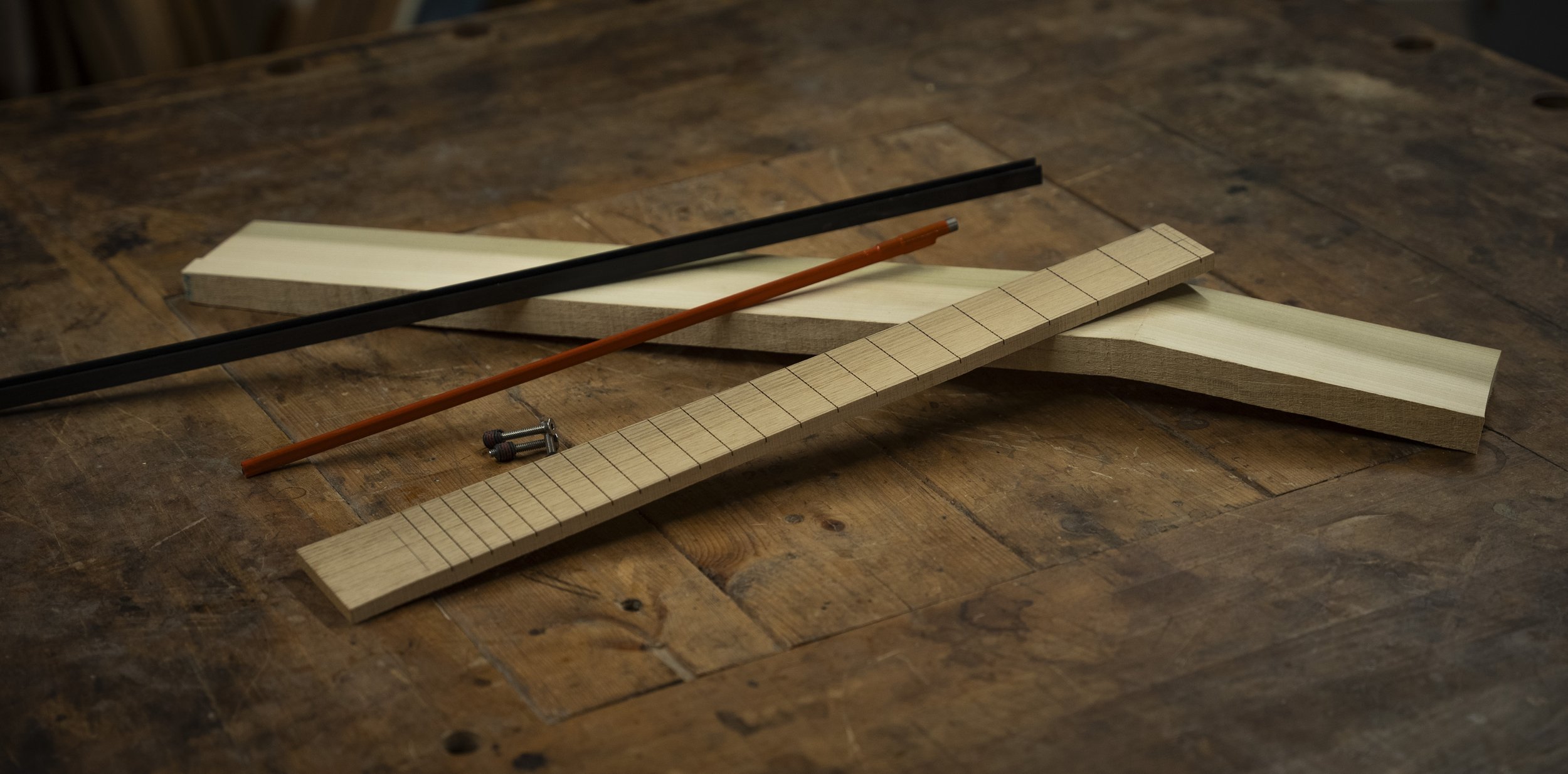
NECK CONSTRUCTION
The neck is arguably the most important part of the guitar.
It’s generally the first interface between the player and the instrument and where first impressions are formed. It’s critical to the feel, playability, and stability of the instrument.
All Island necks start with quartersawn lumber for both the neck and fretboard. I use a proprietary carbon fiber reinforcement that is approximately 400% stiffer than the “standard” practice of placing two rods parallel to the truss rod, and greatly resists torsional stress.
This is paired with a custom steel two-way truss rod that is on average 25% lighter weight than most available truss rods. My necks are exceptionally stiff, stable, and generally very lightweight - depending on wood species, of course. In most cases, they are coupled to the body with machine screws and threaded inserts for both a much stronger connection, but also a much more removable and repairable one.
Necks are meticulously carved entirely by hand over several days. Proper geometry is shaped into the fingerboard and frets are painstakingly seated, shaped, and polished for an unparalleled setup and playability.
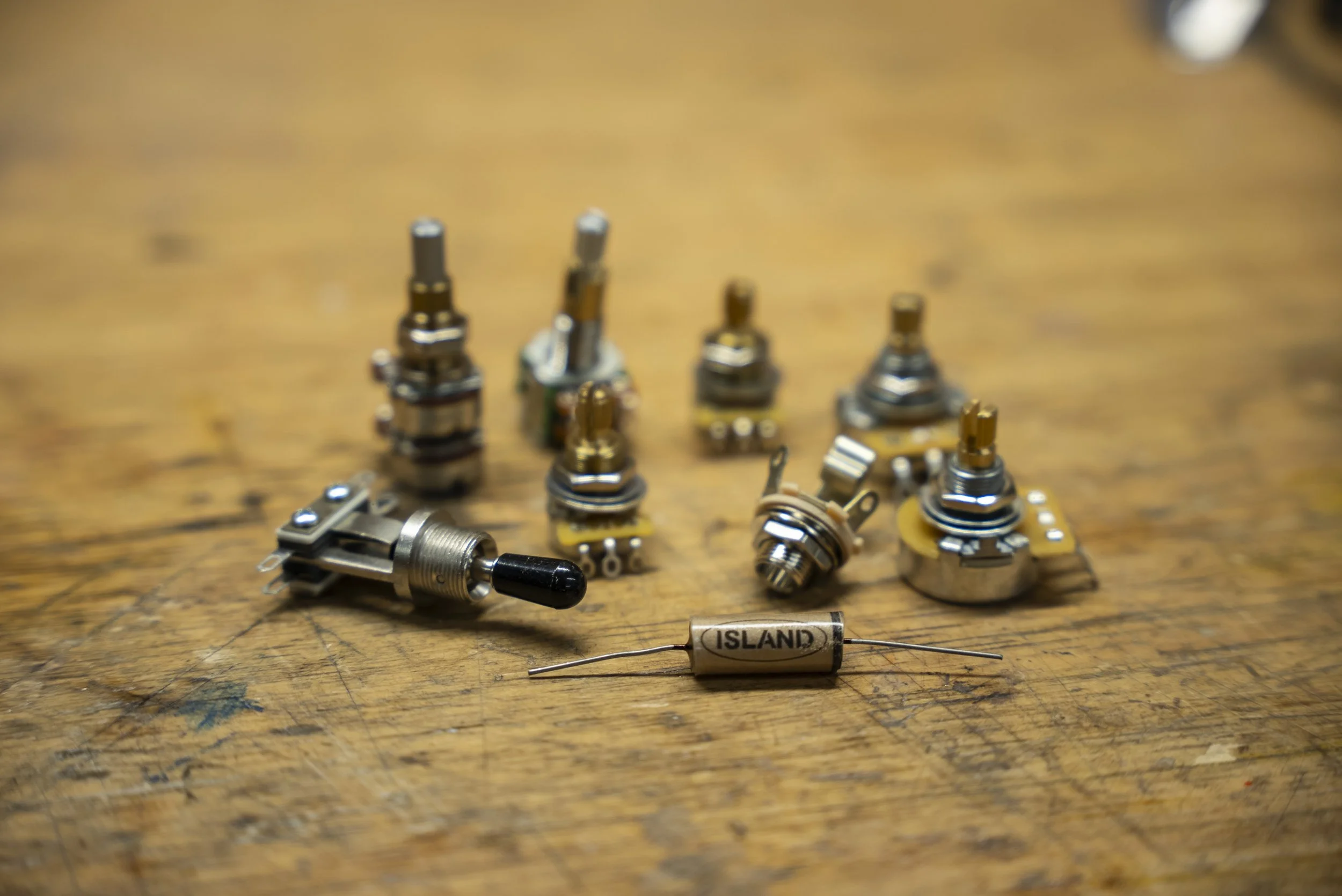
PICKUPS & ELECTRONICS
If wood is the bones of the instrument, the electronics may be the soul.
The proprietary Island Hersheybucker was developed in collaboration with Mojo Pickups in the UK and has been a signature element of my guitars for over a decade.
It is based on the DNA of the old DeArmond Hershey Bars and evolved into something entirely its own and unique.
It is a low-output humbucker that is slightly microphonic. The tone is “wide open” – acoustic, articulate, crystal clear, and full of harmonic information across the whole spectrum. It’s extremely touch-responsive, great at driving a tube amp, and is a wonderful platform for pedals.
Pickups are always paired with the highest quality components from legacy manufacturers like Switchcraft, CTS, and CRL and I use a variety of capacitor types and values depending on the instrument, ranging from vintage NOS to my own custom-made Island TNT tone caps.
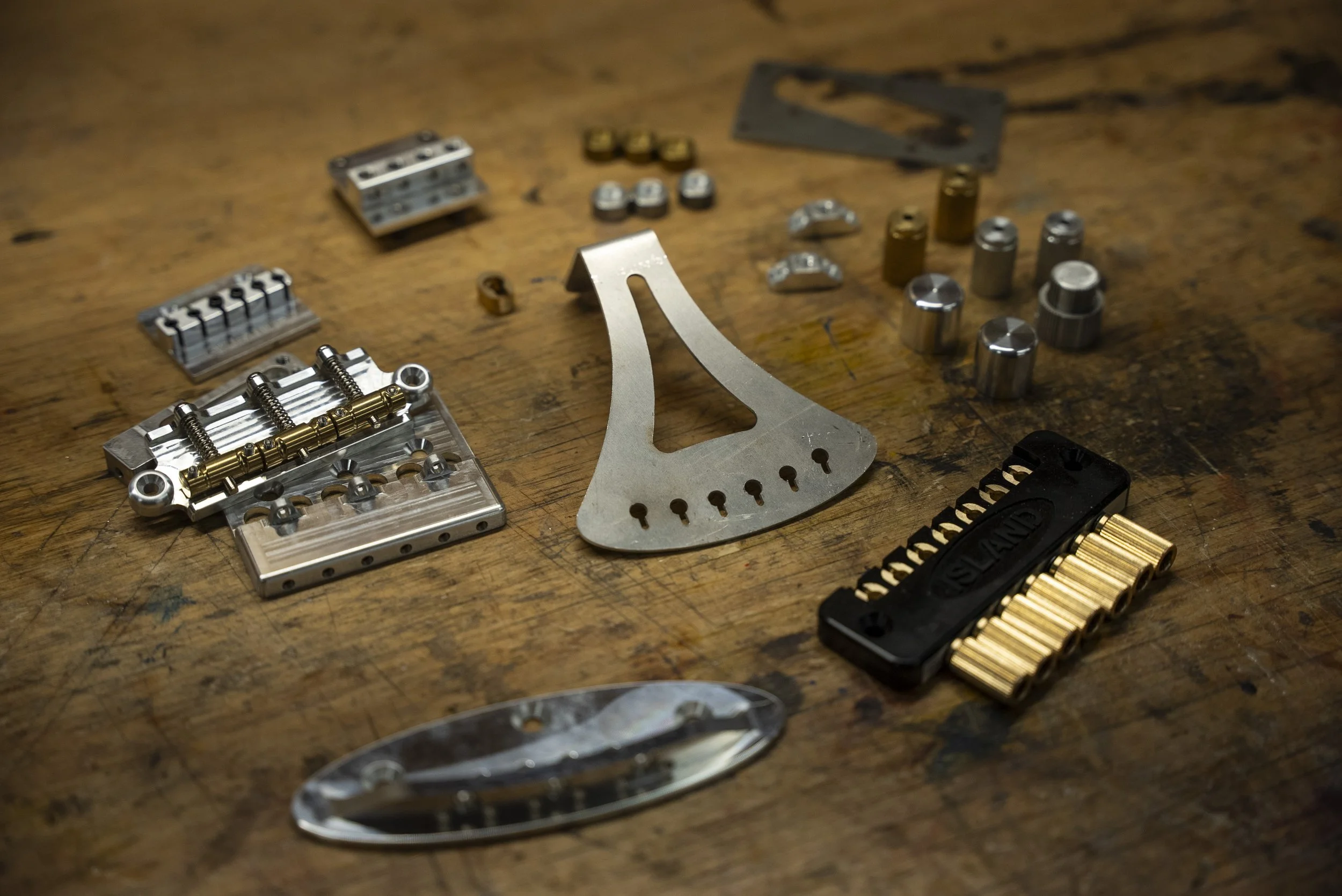
HARDWARE
Obsessively conceiving and constructing a one-of-a-kind custom instrument, only to throw off-the-rack hardware onto it never seemed quite right to me.
I’m just as passionate about parts.
Over the years, I have designed and fabricated many of my own proprietary components from bridges, tailpieces, headless hardware, knobs, pickup covers and more. I’m still constantly thinking of new ideas and working to bring them to life and incorporate them into my builds.
When a project calls for something other than my own designs, I use the highest quality parts from other individual makers, small companies, and high end suppliers.
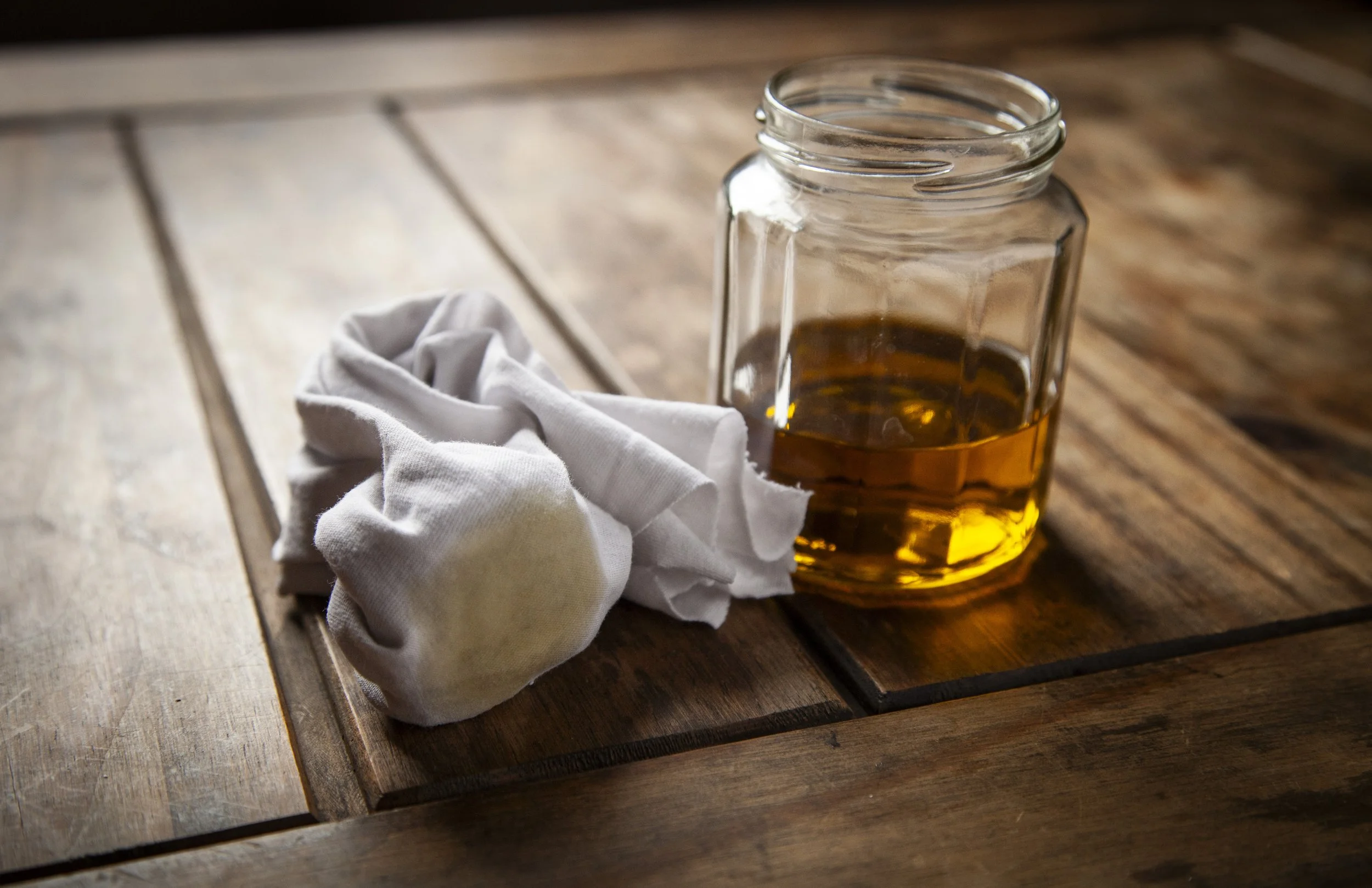
FINISH
Finish has always been considered a critical component to the sound of acoustic instruments, from the violin family to the traditional French Polish of the Spanish classical guitar.
For some reason it was decided along the way that most electric instruments would be finished with a thick (sometimes several millimeters thick) hard plastic-y finish: durability at the cost of feel and resonance.
I use a variety of different paints and finishes on each of my instruments. From my trademark milk paint colours, to hand rubbed oils, shellacs and varnishes, to sprayed lacquers.
They are always extremely thin, open pore finishes, allowing the instrument to breathe, resonate and express itself.
GUARANTEE
Every Island is guaranteed for my life as a working guitarmaker.*
*The guarantee does not cover damage due to accidents, misuse or negligence.
Replacement of parts not manufactured in house are to my discretion.